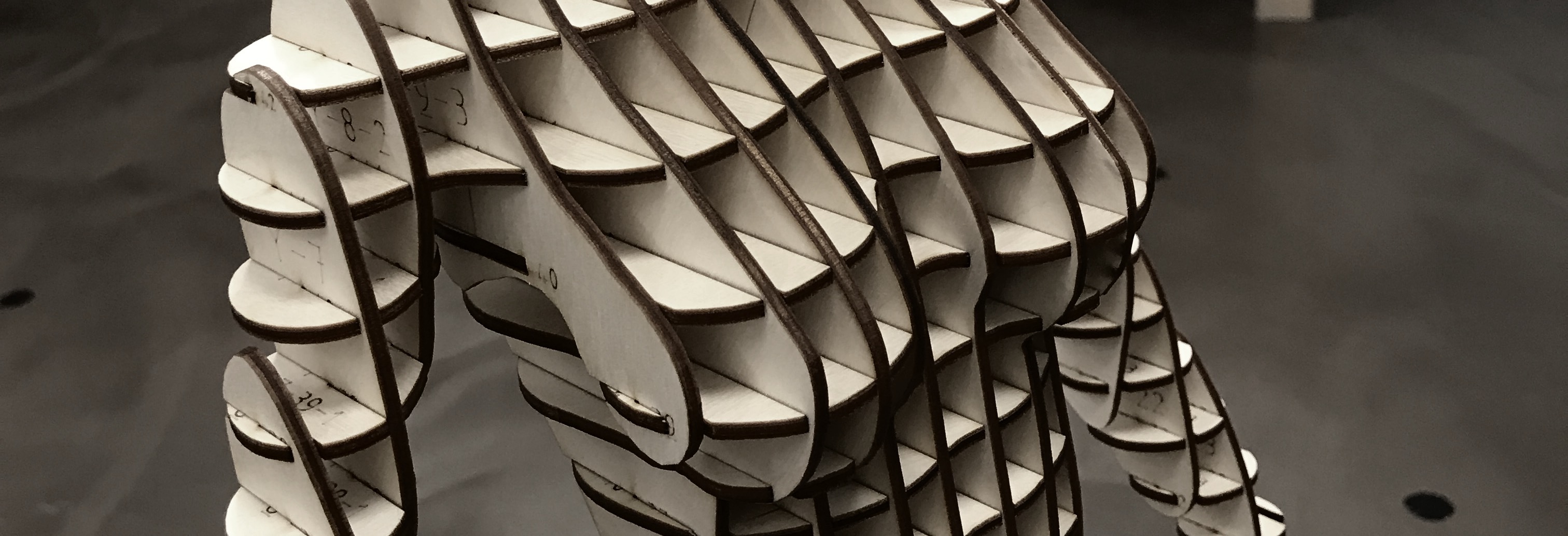
Making mannequin
This first-class week has been so inspiring that I feel the need to make a summary section. I made 2 mains explorations projects link to the idea of the digital body but I had so much more in mind !!! I almost drove me crazy lol !!
The first one is linked to the software Makehuman which I thought was awesome. I had the idea to explore a male and a female type of body and make a quarter of mannequin with them. As I wanted to explore two type of body I thought it'd be preferable to make smaller mannequin. But then, I was modeling those bodies and I thought they were definitely too classic. It's nice to work with clean and lean bodies but the reality is otherwise. So, I created another one that has an untraditional body. Here are some images :
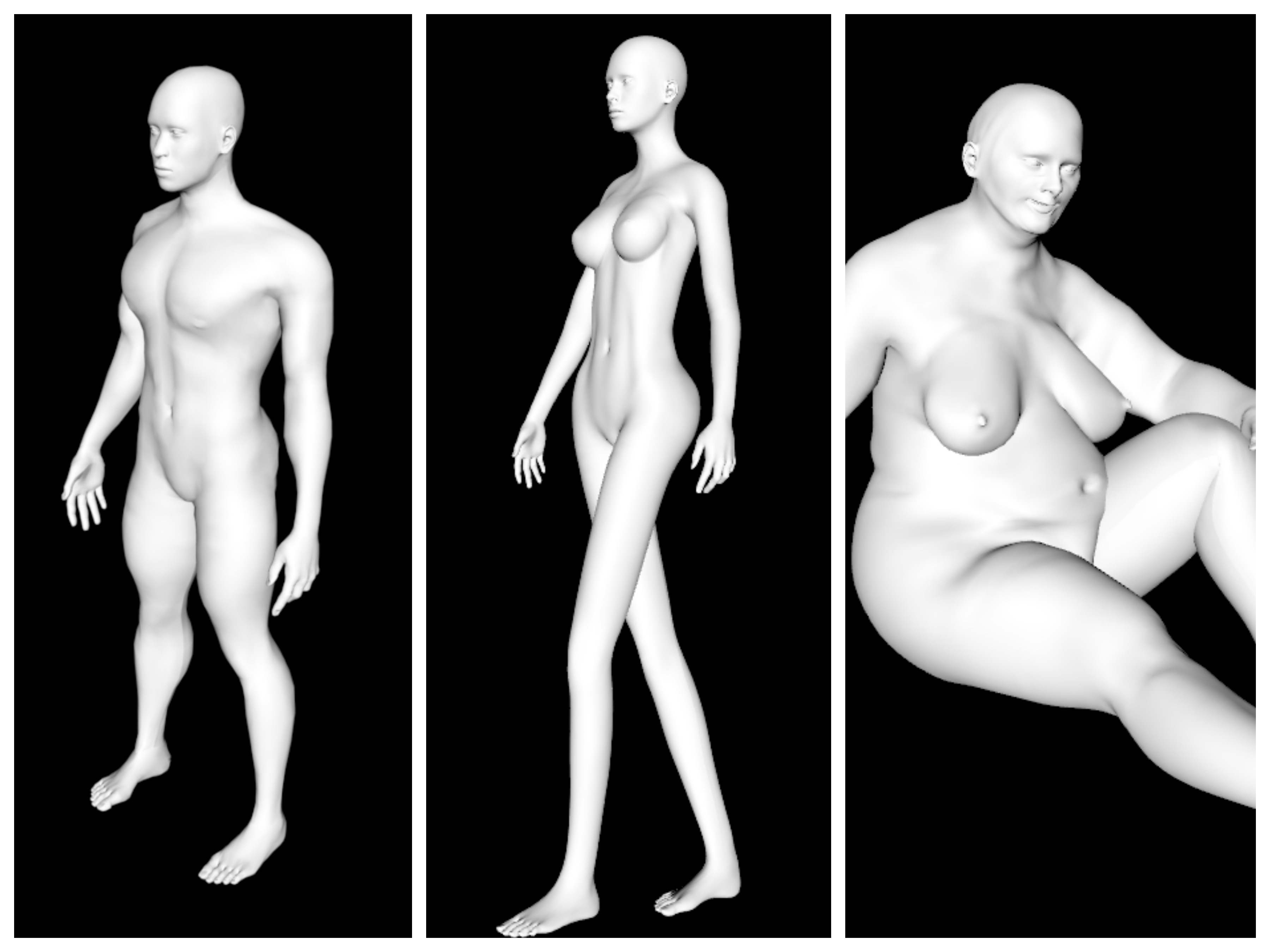
The software gives you so many options to modelize different types of body. That's very cool! Here's some nice feature of the software. But at the end, it's always better to have fun with the software like this one. It is very, but very user-friendly so I guess it's not useful to go through all the process.

The next step was to think about a way to destructure them so I can materialize them. I began with the female mannequin just because. So, I needed to import it in Fusion360 which is the CAD software I like to use. In Fusion, you don't import files but upload them just so you know. Also, it's important to upload a .obj file because the .stl will be all scattered. Then, I used the Slicer for Fusion 360 as a slicer software. At the end, I realized that I could just open the file in the plugin without passing by Fusion360. Then it was time to slice her!
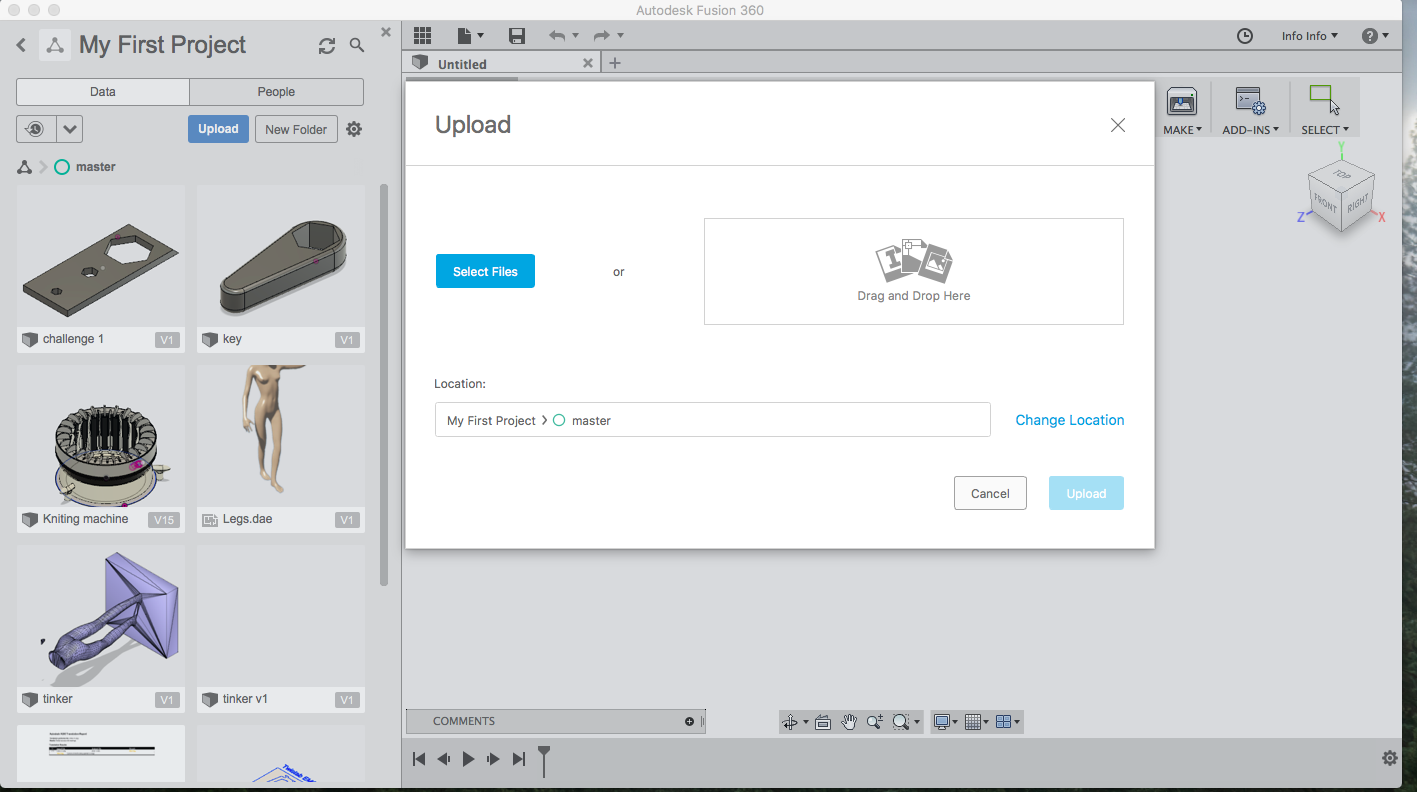

There are two things I need to specify. First, the material size is set as very oversize. I do that because I don't like the nesting it produces. There's always too many losses in them. Also, you'll see that the final model as errors in it. Looking closely at them, it seemed to me that they were not important and very small. So I decided to do it anyway. In brief, don't trust the nesting and the error marks, look at them yourself.
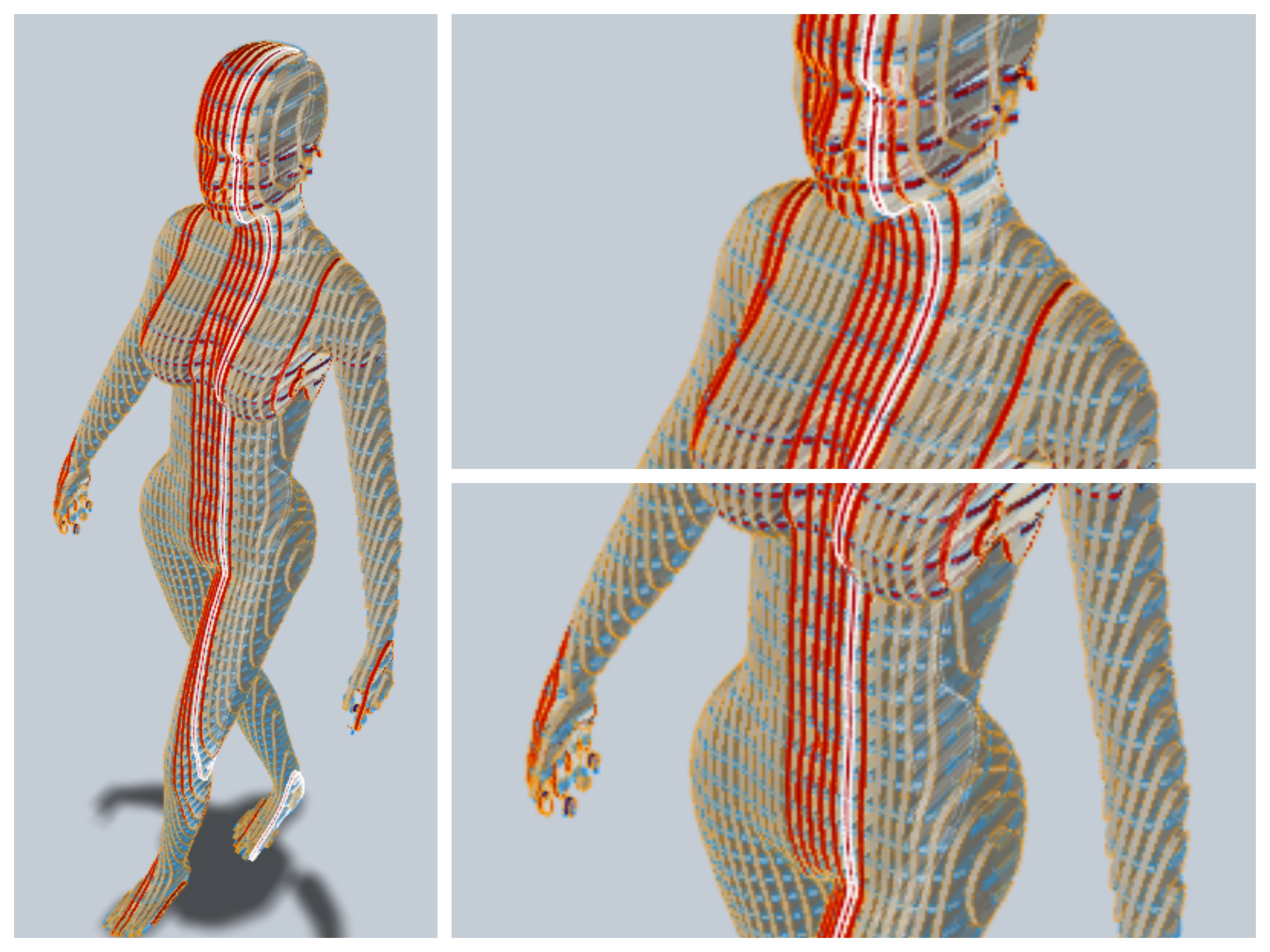
Then, I laser cut the whole thing. It took me 4 plates of 17"x29" to fit the project using the laser cut I have in the lab. Then, I assembled the pieces. It took a long time but wasn't as difficult as I thought. I usually do those structure with cardboard which is much more flexible. Plywood is stronger and easier to assemble. The result was very nice.
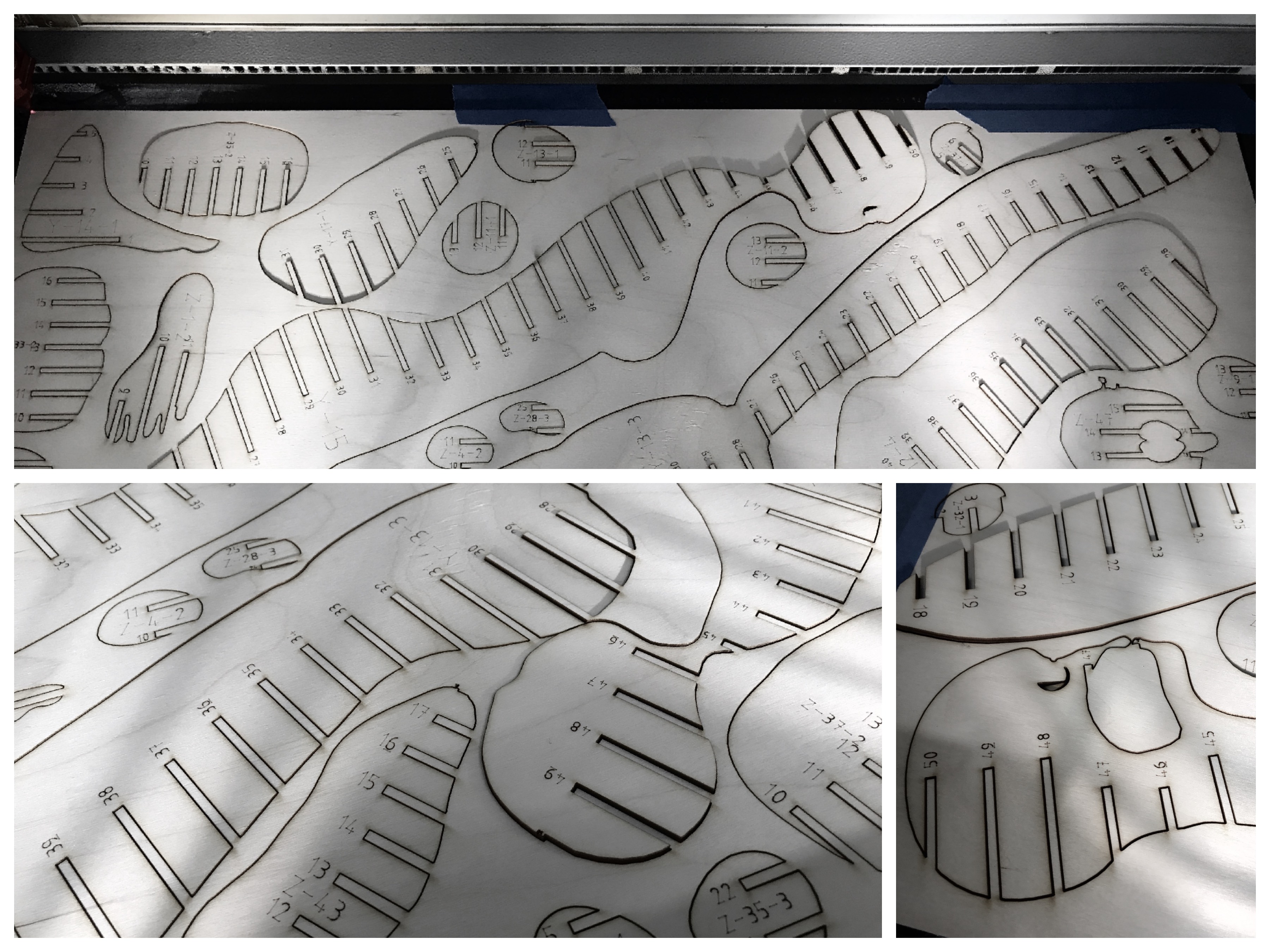
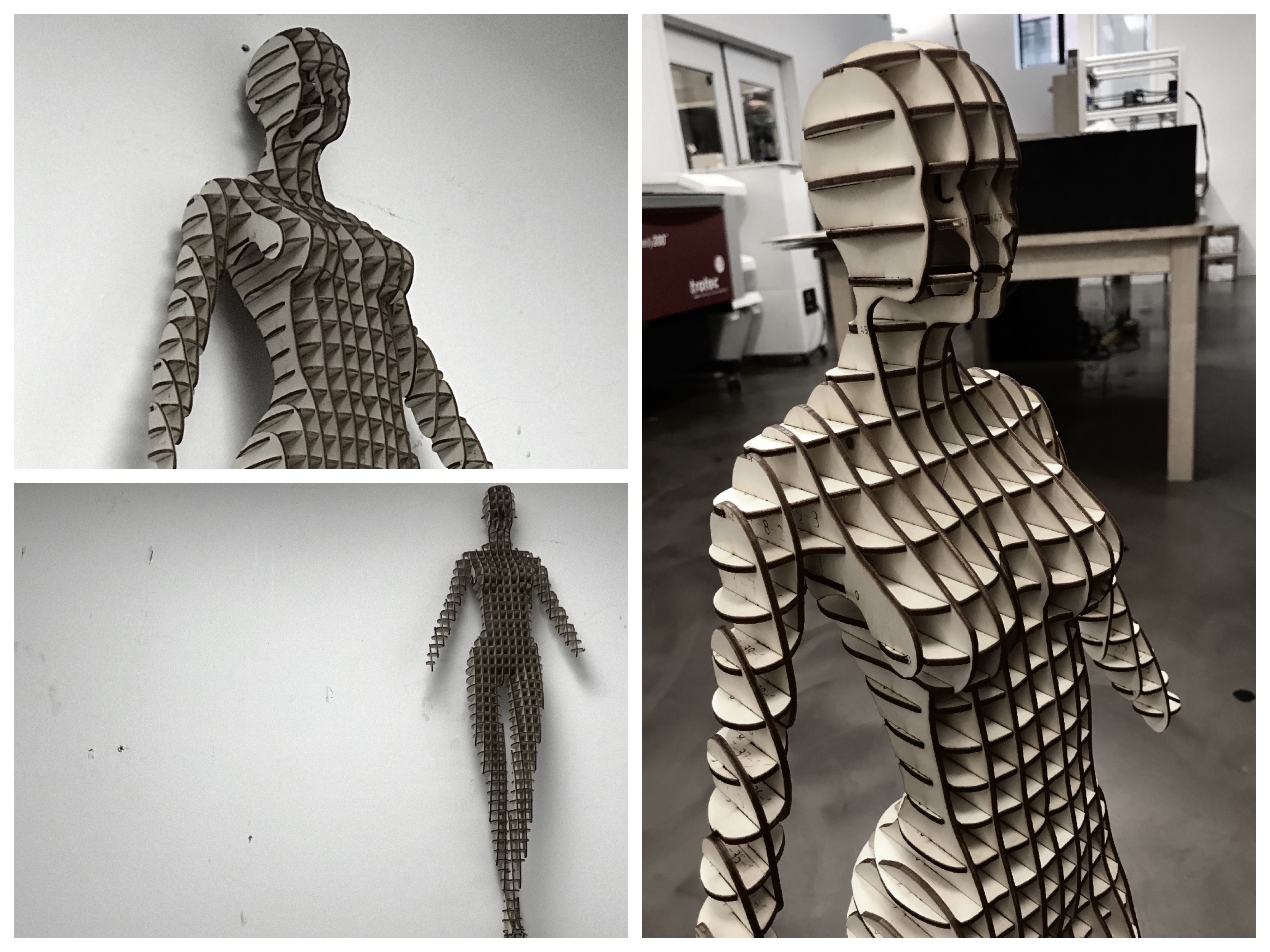
But, because there's a but ! I didn't plan a base so she can stand up. And yes, in the lecture instructors adviced us to do so. God damn ! I decided to hang her on the wall instead. Just over my brand new wetlab that I set.
Still, I wasn't satisfied, I wanted to do more. So I decided to make the male mannequin with a base this time. I encounter one challenge, when I imported the .obj file in Fusion 360 it took the shape of a mesh file, which is normal but the base I built was a solid and I could not find a way to export them to the slicer together. I was like if they were not connected together. Which seemed obvious considering that they are completely different information about the software. I found some solutions on the web but never exactly what I was looking for. At the end, I took ThinkerCad and add the base there so I can export it in .stl and put it back in Slicer fro Fusion360. Another but is that I didn't figure well the size the base would take and it's very massive. Beautiful but massive !!! I then laser cut the pieces and assembled it. It took me 6 hours to do it and was a pain. That was enough so I didn't make the last one :p. Well, I guess that two is enough!
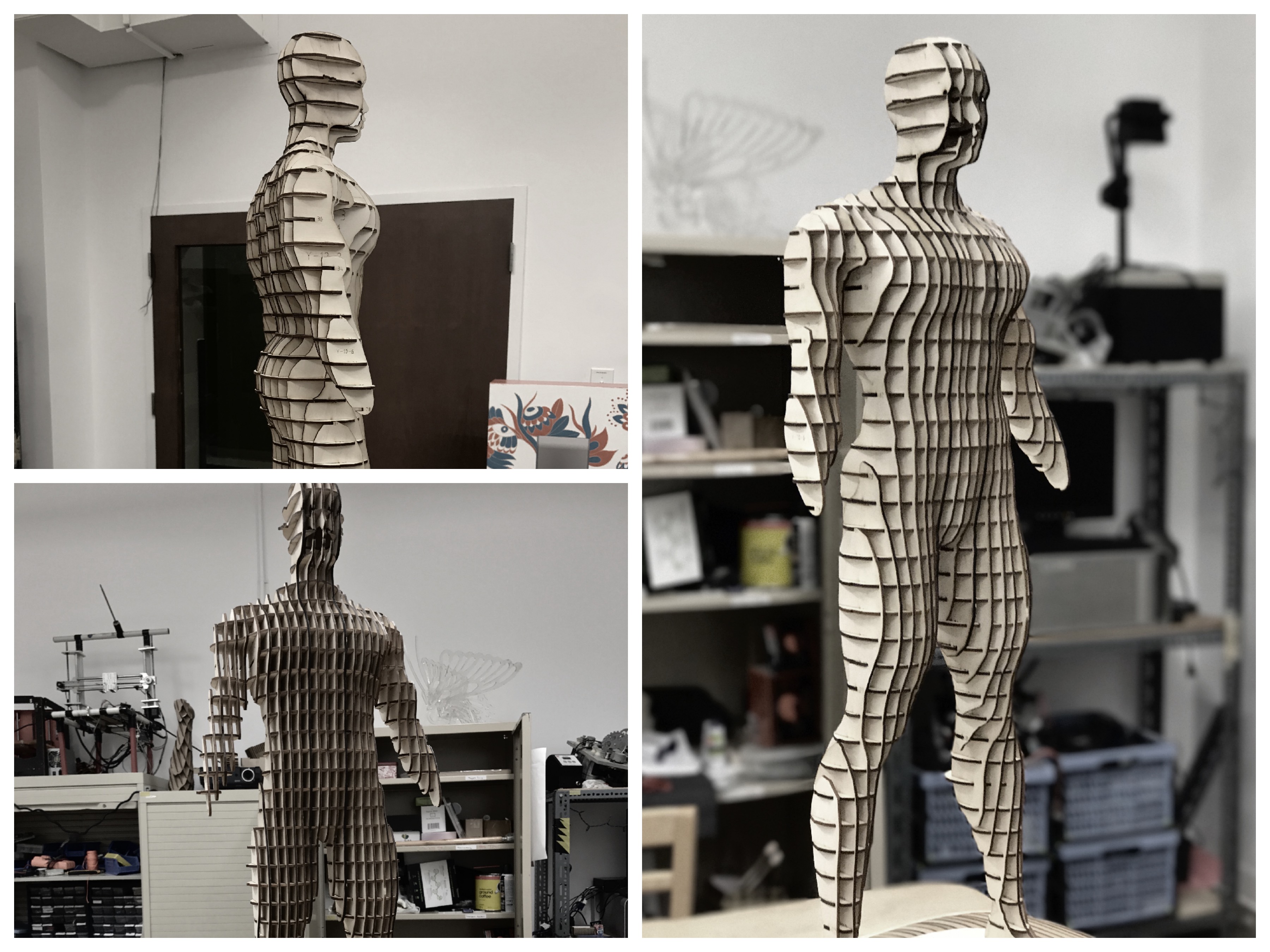
All the files are available if anybody wants do make one.
Scanning human body parts
But then, is building those enough? I don't know but I wanted to explore another technic and a more concrete one I thought. I wanted to scan a body part to have that digital representation of it. The 3D scan I used is a Sense. Really easy to use and userfriendly. To me, it works well for body or big object but when it comes to a small object it's more a headache then anything. Each time I used it with a lab's user to scan small object, I finished by modeling the piece with Fusion360 instead.
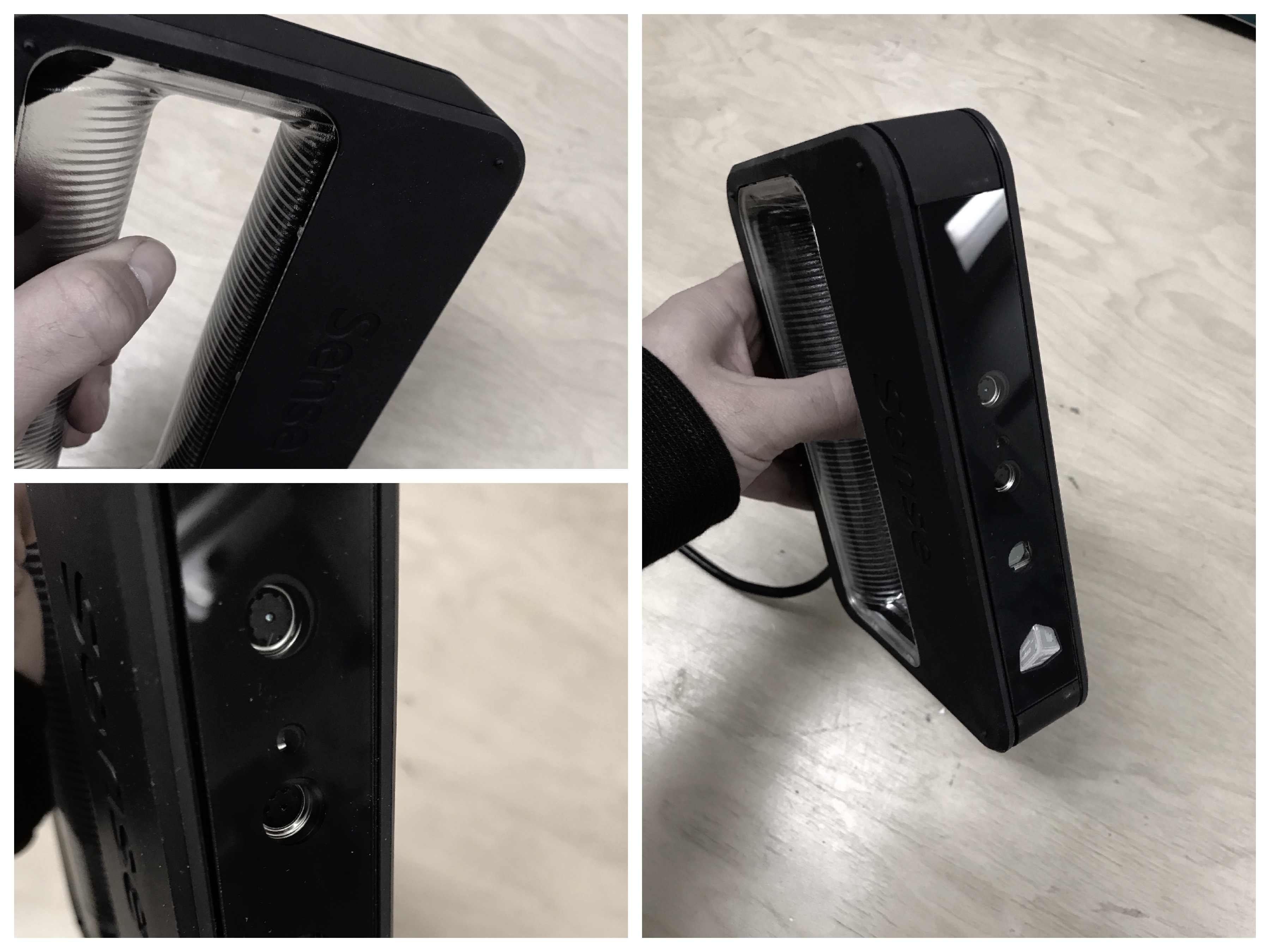
It's almost plug and play so it's kind of easy to use. Be careful to set the right object size because the box created by the software will constrain you. Also, it's very easy to lose the track so go slowly. The most time you pass on parts the better it'll get. It's also very bad with small objects. Be patient!
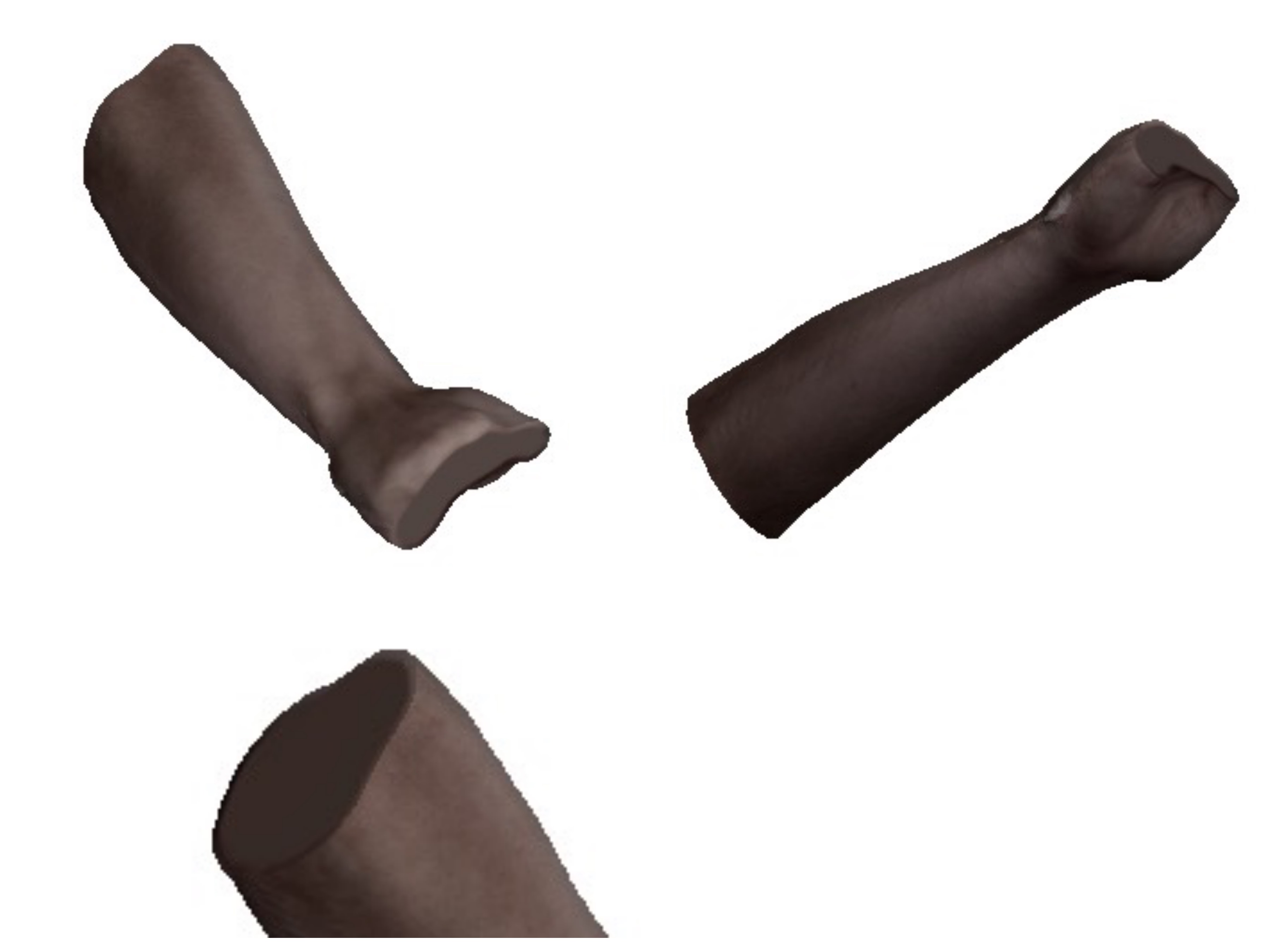
The result was pretty clean. Skins are scanning very well. At the end, I just filled the scanned arm and clean just a little bit with the existing tool. The thing here is that I really hate working with mesh. There something to close to sculping happening with mesh modeling approaches. It obviously a valid approach but my mind prefers working with solids and parametric design. I tried ti use meshmixer and hated the experience from beginning to the end. Then, I tried working with Fusion 360. The software has a mesh working so I tied it because I still wanted to clean a little bit the piece.
At the end, I exported it to and .stl file. What's nice with that it that I now have a virtual interpretation of her body so I could create a completely personilized object for her.
So, you can import a .stl file and then, in the "sculpt" section you can modify the mesh with the proposed tools. What's great too is that you can convert the mesh into solid and then, in my opinion, make the work much easier.
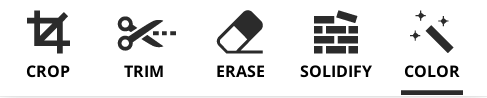
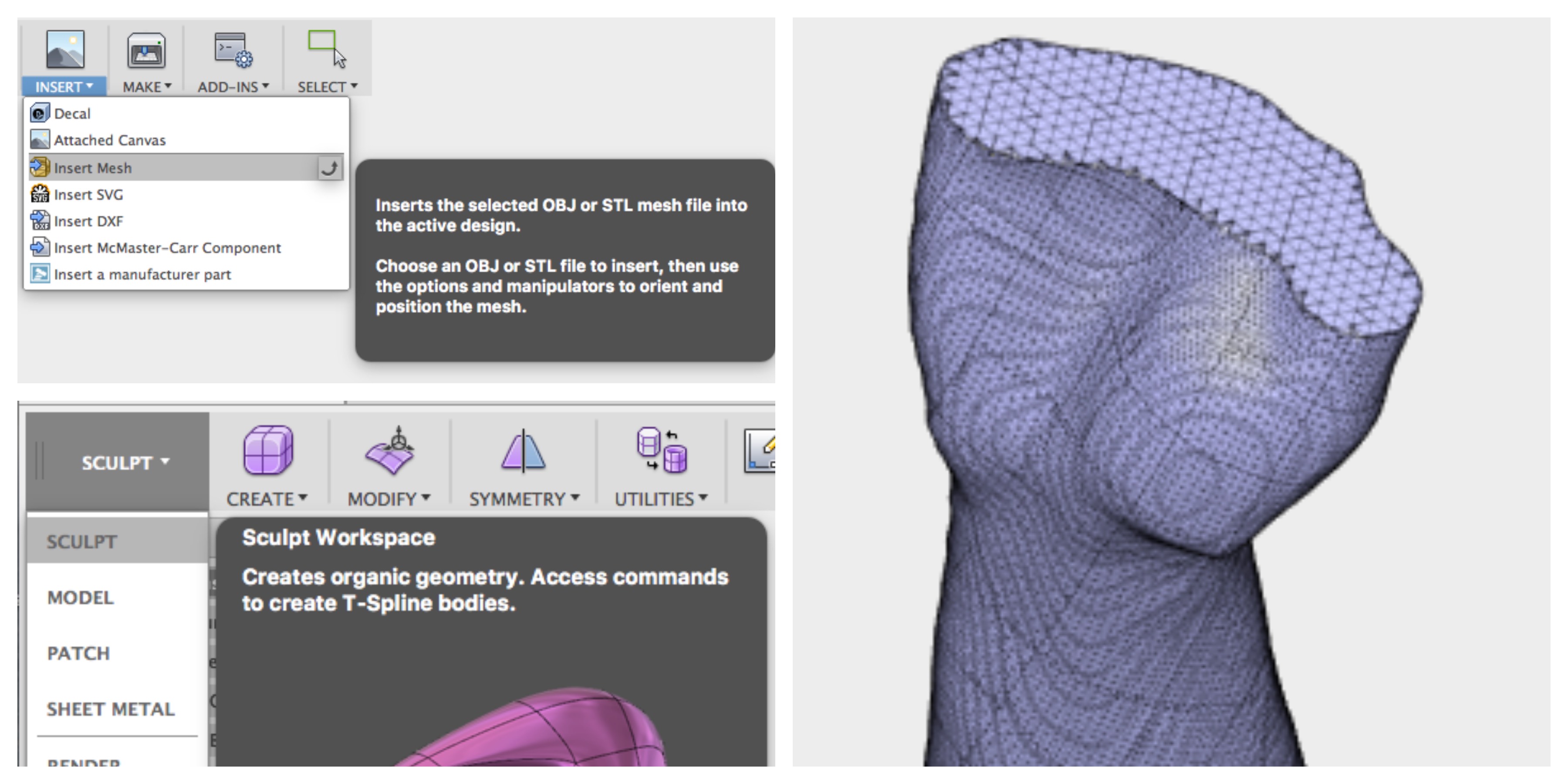
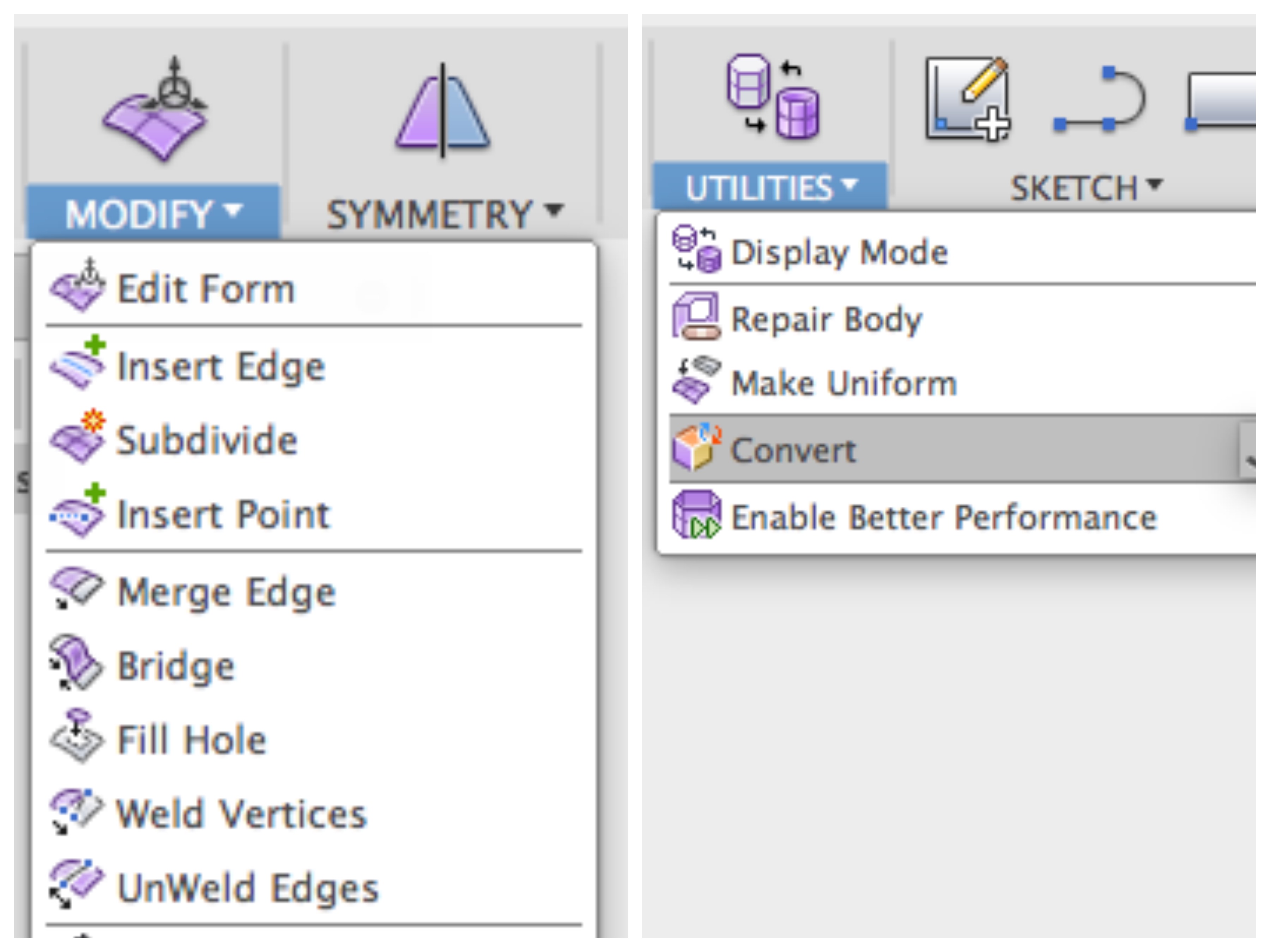
I also wanted to materialize whole thing with the slicer just because I like it ! :p Here's the result !
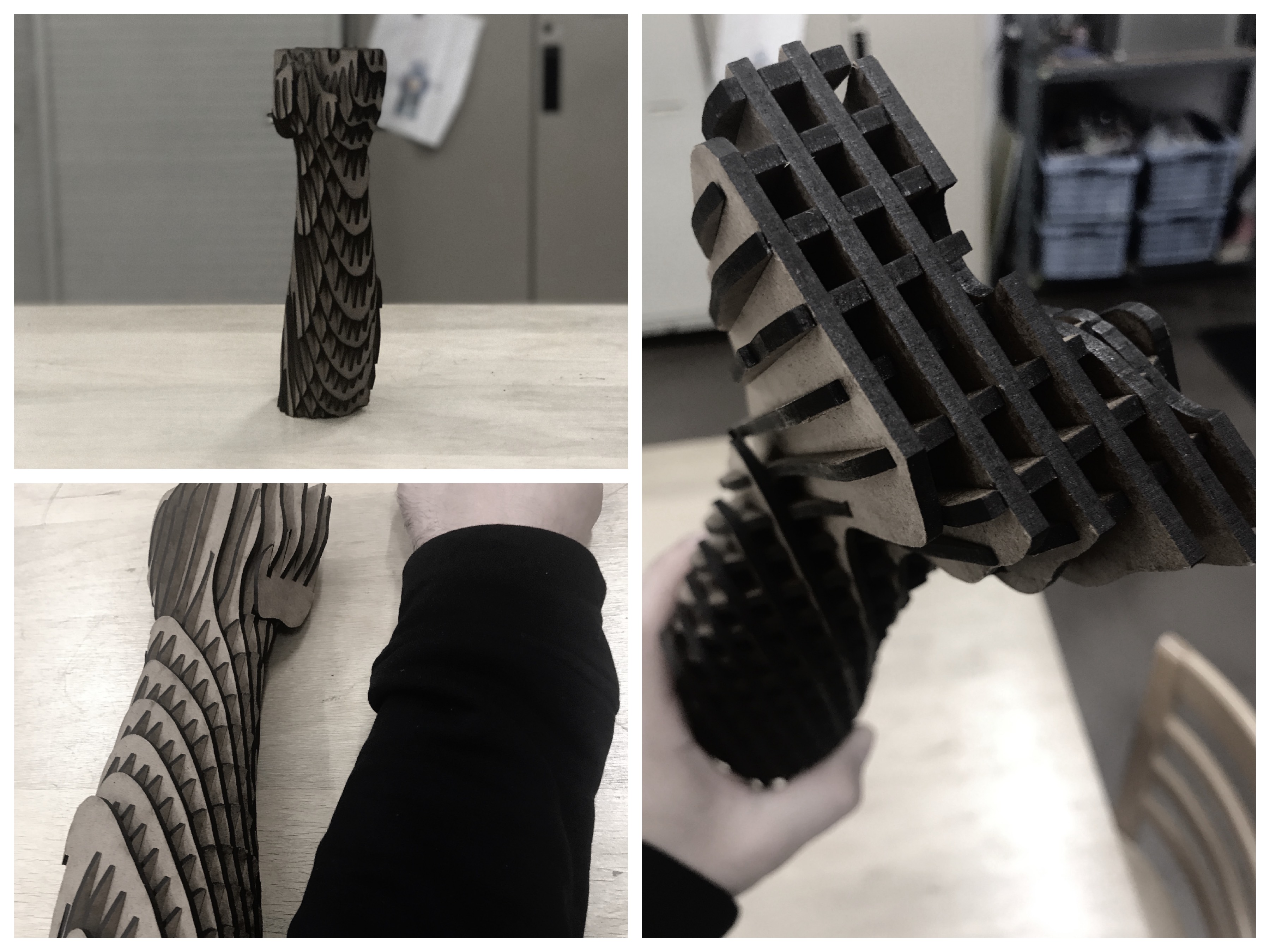